Business Operations Management (BOM) is a fundamental aspect of any organization, responsible for overseeing, and controlling the activities that contribute to the production of goods and services. At its core, Business Operations Management is the management of the processes and systems that create and deliver a company’s products or services.
It encompasses everything from managing supply chains and overseeing production to handling logistics, workforce, and technology systems. This discipline involves coordinating resources—such as people, equipment, technology, and finances—to produce goods or services efficiently.
Main Components of Business Operations Management
- Process Management: This involves analyzing business processes to improve efficiency and effectiveness.
- Supply Chain Management: This involves procurement, inventory management, and logistics. A well-managed supply chain ensures that materials are available when needed and that products reach the market on time.
- Resource Management: This entails allocating and managing the business’s resources e.g human, financial, and technological. Effective resource management ensures that the right people, equipment, and technology are in place to meet the company’s objectives.
- Quality Management: Quality management involves setting quality standards, implementing quality assurance processes, and monitoring output.
Technology Integration: In today’s digital world, technology plays a crucial role in business operations management. Integrating tools like Enterprise Resource Planning (ERP) systems, Customer Relationship Management (CRM) software and other automation solutions helps improve accuracy, and provide valuable insights through data analysis.
Objectives of Business Operations Management
- Efficiency
- Quality
- Flexibility
- Innovation
- Customer Satisfaction
Business Operations Management is not just about managing day-to-day tasks; it’s about strategically overseeing the entire operational framework of a company to ensure sustainability, profitability, and customer satisfaction.
Key Roles and Responsibilities of a Business Operations Manager
A Business Operations Manager plays a crucial role in ensuring that a company’s day-to-day activities align with its long-term goals. This position is central to the smooth functioning of an organization, bridging the gap between upper management’s strategic vision and the actual implementation of policies and processes within the workplace.
- Overseeing Daily Operations
- Process Improvement and Optimization
- Managing Budgets and Resources
- Strategic Planning and Goal Setting
- Team Leadership and Development
- Coordinating Cross-Departmental Efforts
- Monitoring and Reporting on Performance Metrics
- Ensuring Compliance and Risk Management
- Managing Customer and Vendor Relationships
- Driving Innovation and Change Management
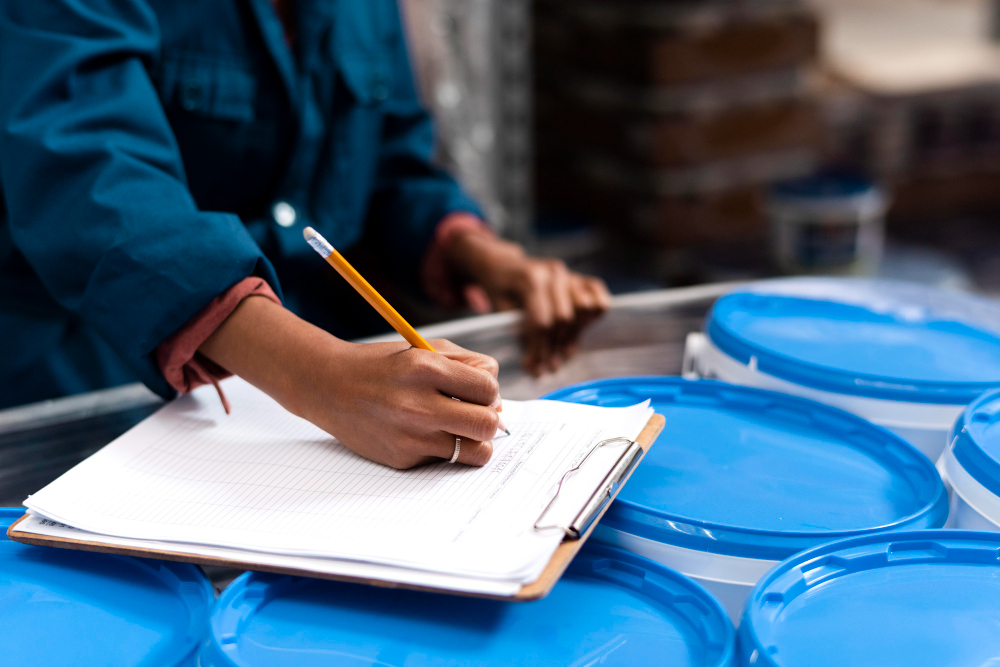
Skills Required for a Business Operations Manager
- Analytical Skills: Ability to interpret data, identify trends, and make data-driven decisions.
- Leadership: Strong leadership skills to manage teams, resolve conflicts, and drive projects to completion.
- Communication: Effective communication for coordinating with teams, stakeholders, and clients.
- Problem-Solving: Capability to quickly identify problems and implement solutions.
- Financial Acumen: Understanding of budgeting, cost management, and financial analysis.
- Technical Proficiency: Familiarity with business management software, tools, and technology e.g OTAWISE.
What is Production Management in Business?
Production management in business is the process of planning, coordinating, and controlling the various activities involved in producing goods or delivering services. Effective production management is crucial to the success of any business, as it directly impacts quality, efficiency, costs, and profitability.
Key Components of Production Management
- Planning: This is the initial stage of production management, where strategies are developed to meet production goals. It involves determining what to produce, when to produce it, and how much to produce.
- Scheduling: It involves setting start and end dates for each phase, coordinating with suppliers, and allocating resources effectively.
- Quality Control: It involves setting quality benchmarks, monitoring production, and conducting tests to identify and rectify defects.
- Inventory Management: It ensures that there is enough inventory to meet production demands without incurring excessive holding costs.
- Production Process Optimization: This involves analyzing and refining the production workflow to increase efficiency.
- Cost Control: Cost control focuses on managing production expenses to keep them within budget. This includes monitoring material costs, labor costs, and overhead expenses.
Role of Technology in Production Management
Technology plays a pivotal role in modern production management. The use of business management software and automation has revolutionized how businesses handle production.
- Automation: Automation involves using machines, robotics, and software to perform repetitive tasks. This reduces the reliance on manual labor, speeds up production, and minimizes errors.
- Business Management Software: Business management software like ERP (Enterprise Resource Planning) systems integrates various aspects of production management, including planning, scheduling, inventory, and quality control. These tools provide real-time data, allowing production managers to make informed decisions, track progress, and adjust processes on the go.
Importance of Production Management
- Efficiency and Productivity
- Cost Reduction
- Quality Assurance
- Customer Satisfaction
- Competitive Advantage
The Relationship Between Business Operations and Production Management
Business operations and production management are two closely interconnected components that play a critical role in a company’s overall efficiency and success. it’s essential to explore how these two aspects align and impact the functionality of a business.
Understanding the Core Connection
Business operations management focuses on overseeing all the functions and processes that make a business run smoothly. On the other hand, production management deals specifically with the manufacturing process or the creation of products and services. It focuses on the efficient use of resources to produce goods at the right time, in the right quantity, and at the right quality.
The connection between these two areas lies in their shared goal: efficiency. While business operations management covers a broader scope that includes all aspects of the company, production management is often seen as a subset within operations, dedicated to the actual production of goods and services.
Aligning Production Goals with Business Objectives
A key aspect of the relationship between business operations and production management is alignment. Effective business operations require that production goals are not only well-defined but also closely aligned with the company’s broader objectives. For example, if a company’s objective is to reduce time-to-market for new products, the production management team needs to adopt lean manufacturing techniques, automate processes where possible, and reduce production bottlenecks. This alignment allows businesses to respond more swiftly to market demands and remain competitive.
Case Studies: How Companies Benefit from Aligning Operations and Production
Apple’s Operational Excellence in Product Launch: Apple aligns its production management with its business operations by carefully controlling every aspect of the supply chain. From sourcing materials to manufacturing and logistics, Apple’s operations team ensures that the production management aligns with product launch schedules and quality standards. This results in successful product rollouts and maintains Apple’s reputation for quality.
Challenges in Integrating Business Operations and Production Management
Communication Gaps: Effective collaboration requires clear communication channels and real-time data sharing, otawise is a cost friendly option in this regard.
Balancing Quality and Efficiency: Sometimes, the drive for efficiency in production can compromise quality, which can negatively impact overall operations.
Managing Complexity: As businesses grow, their operations and production processes become more complex. Managing this complexity requires sophisticated software tools, automation, and constant monitoring.
Tools and Technologies Bridging the Gap
Modern business management software plays a crucial role in integrating business operations and production management. Some key technologies include:
ERP Systems (Enterprise Resource Planning): These systems help businesses integrate production management with other operations like finance, HR, and supply chain.
Project Management Tools: Tools like Trello, Asana, and Microsoft Project enable better coordination between operations and production teams.
CRM Software: tools like otawise enable better communication with clients and staff.
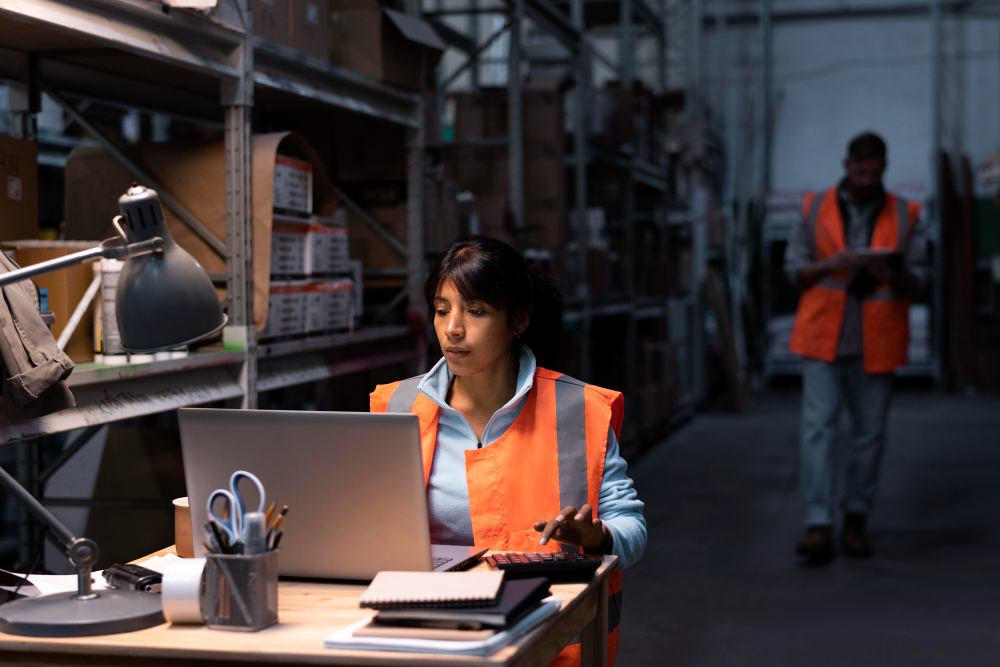
How Otawise Business Management Software Supports Operations and Production
Managing the complexities of operations and production can be a daunting task without the right tools. This is where Otawise Business Management Software comes in, offering comprehensive solutions to streamline both business operations and production management. Below is a detailed look at how Otawise can transform these critical areas.
Streamlining Business Operations: The software is designed to simplify and automate various facets of business operations. It integrates essential management functions into a single platform, allowing companies to coordinate tasks, track progress, and optimize workflows. Here’s how it supports business operations:
- Centralized Data Management
- Automation of Routine Tasks
Scalability and Flexibility: One of the standout features of Otawise is its scalability. Whether you are a small startup or a large enterprise, Otawise can be tailored to fit your specific needs. It grows with your business, offering more advanced functionalities as your operations and production requirements evolve
- Customizable Modules
- Cloud-Based Access
Cost Efficiency and ROI: Investing in business management software like Otawise leads to long-term cost savings and improved return on investment (ROI).
Here’s how:
- Improved Productivity
- Reduction in Operational Costs
- Better Resource Utilization
Conclusion: Why Choose Otawise for Business Operations and Production Management?
Otawise stands out as a robust business management software that empowers companies to optimize their operations and production processes. Its all-in-one solution offers features that enhance productivity, cut costs, and improve overall efficiency. Whether a business is small or large, Otawise provides the tools needed to thrive in a competitive market.
By implementing Otawise, businesses can expect smoother operations, efficient production, and a more proactive approach to management—all of which contribute to long-term success.
RELATED READ: Top 3 Document Management Tools for Nigerian Businesses
RELATED READ: 6 Best Workflow Management Software for Nigerians.